Blog
Beat the Manufacturing Competition with a Low-Cost Way to Improve Products
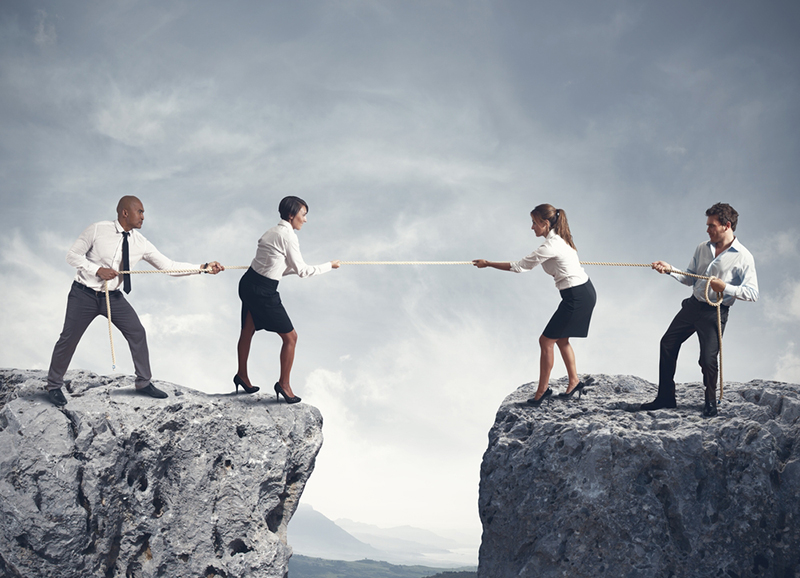
In the manufacturing business, a competitive edge can be hard to achieve through product improvement. Companies usually invest in large-scale research by top scientists, designers, and engineers to improve their products. Huge costs are incurred, and as a result, gaining a competitive edge becomes an expensive challenge for most.
Scientific and market research can help you gather valuable information, but there is a cheaper way to improve your products. It starts with problem identification and leads to relevant changes in your manufacturing process. If you offer warranties on your products, there is a vast market to provide you with data about defects and anomalies. Every time a warranty issue arises, you have the opportunity to find relevant data and work on improvements.Such data obtained through the warranty process is sizeable and gives you a great opportunity to learn about product problems in detail. Analyses will also be more effective than what you can achieve by focusing on a particular prototype. The question is, how does it work?
Technology is the Key
You need a process that can make data collection and analysis cost-effective and time-effective, irrespective of geography, product type, and user request. Manufacturing companies usually have geo-centric service units to reduce service turnarounds. Such units can be equipped with an integrated mobile app to inspect, report, and update you on product issues. The process should help you analyse your products’ problems easily. Usually, the criteria for reporting should be set according to how a particular product functions.
Problem reporting
The first data you collect, even before the service unit is dispatched, is the problem as reported by the user. This may be non-technical data, but it gives you a view of how the customer has been affected. Such data can be entered through an electronic interface nowadays and updated at your end in real time. It makes the process quicker and less cumbersome. The same entry can be logged by your customer service if the user prefers to call in to report the problem.
Technician’s role
Once you identify the problem and what possible solution can be offered, you will be sending a repair and service team to the user’s location. Equip the team with a mobile interface for reporting the problem with all the technical details. These details can be uploaded to your system and transferred to your database in real time. The analysis of your product can begin with the data. If you already have fault-related data, the new data can be integrated with it into one database for seamless analysis.
Root cause analysis
The technology system will let you work on the repair service’s inputs, assign fault codes, and process the data to help in the root cause analysis to be performed later. In order to make sense, you need a strongly integrated system that categorises your products’ problems, maintains consistency between targets, and generates relevant indications to make your analysis a cost- and time-effective one. Through automation, you can achieve a lot!
Expensive implementation of such a system cannot be accepted, especially because this approach is meant to improve product quality in a cost-effective manner. That is when attempts at product improvement are going to have the desired effect.
Competing by banking on your product’s quality and performance is a matter of continuous improvement. Surveys, questionnaires, and other types of customer interactions can fetch a vast range of data to help you improve product manufacturing.
Look for a system that can be deployed according to your specific needs. That said, it is always better to opt for technology that integrates with the useful parts of your existing system without replacing it completely.
NetProphets Cyberworks is a renowned IT company known for its ethos of continuous improvement and successful project completion. The trusted firm specialises in mobile application development services for manufacturing firms aiming to gain a competitive edge. Their innovative approach emphasises leveraging warranty claim data and utilising technology to streamline issue reporting via mobile apps. This cost-effective method facilitates real-time data collection, enabling efficient problem identification and root-cause analysis. NetProphets Cyberworks’ seamless integration and tailored solutions align, offering manufacturing companies an affordable means to enhance product quality and performance.
Author Bio:
Ashley J. is currently a senior business architect with the service operations practice at a well-known IT industry. She has worked on several process improvement projects involving multi-national teams for global customers. She has over 8 years of experience in warranty management systems and has successfully executed several projects in logistics management, logistics integration, reverse logistics, warranty software, and programmatic solutions.
You may like to read this
-
Admin April 28, 2017
8 Vital Signs for Custom Software Development in Your Company
Today, industries all over the world are growing at a tremendous speed. In this fast-evolving environment, it is difficult to single-handedly manage people, expenditures, and operations. However, customised software or an app has the ability to do that. For any growing business, customised software ...
-
Admin March 29, 2016
Expand Your Business with a Custom App
Before you know how you can expand your business via an app, you first need to know a few basic things, such as “What is application development?” and “What are its benefits for business?” and so on. According to eMarketer, the number of smartphone users in the world in 2016 was about 2 bill...